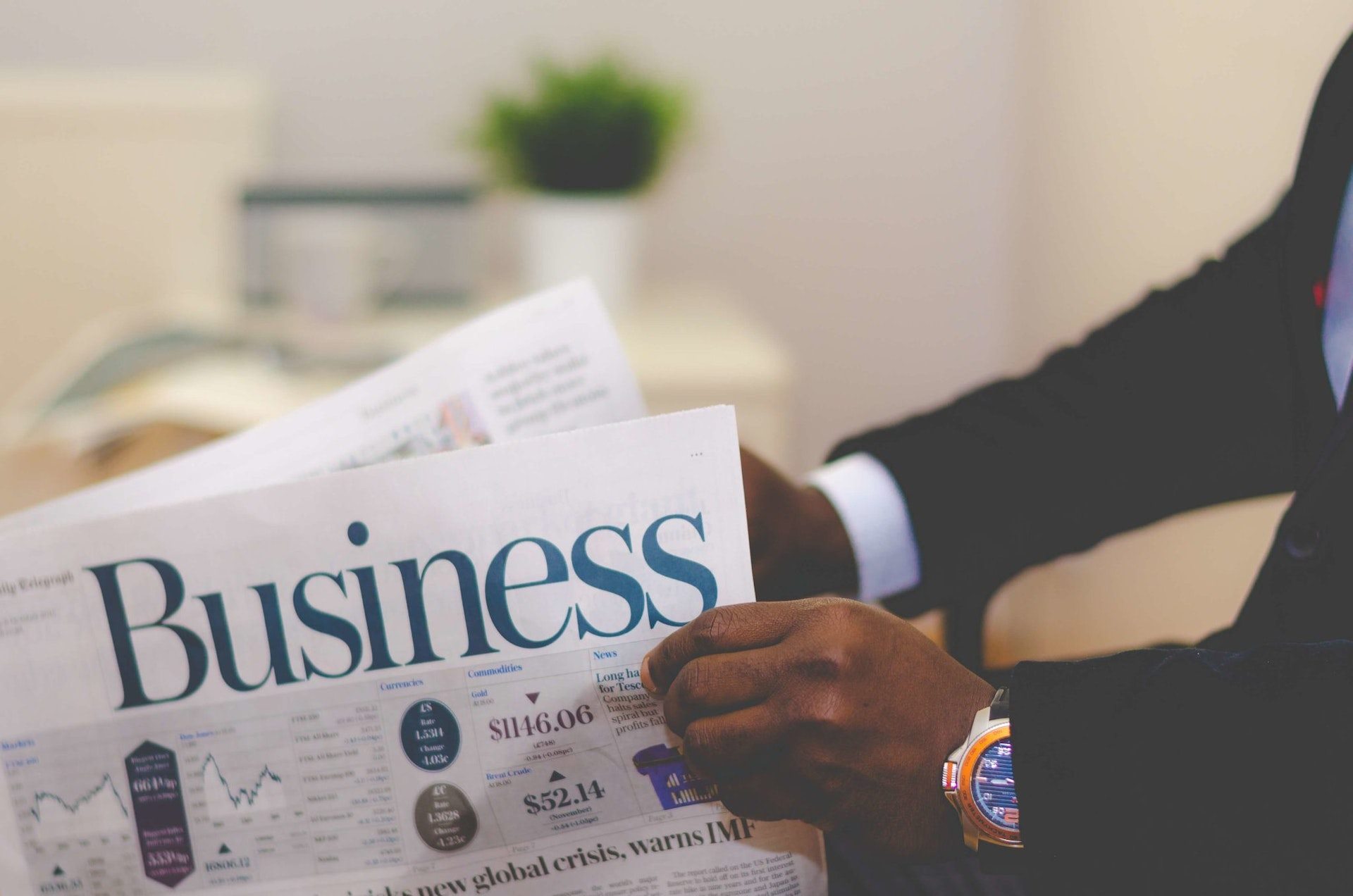
ID智能电动执行机构优化
一、优化的背景
一厂目前以Al/MI智能型电动执行机构为主打产品,但其存在机械结构复杂、加工成本高等缺点,随着市场竞争的同益激烈,产品价格越来越低,利润率逐渐下降,而且价格高造成投标中没有优势。
ID智能电动执行机构已经在2004年开发了样机,但在后续的投产过程中发生了一些问题,作为第一代投向市场应用的三相大力矩执行机构,还存在很多不成熟的地方,所以当时用较成熟的引进的A/M型产品上进行了智能化改造,获得了成功,ID产品暂时被搁置。但从总体上来看,ID产品比Al/Ml产品有优势,ID智能电动执行机构结构相对简单,成本低,从控制角度来看,与Al/MI差别不大,而且体积小,力矩大,价格低,用户更容易接受。
目前十一厂正F在努力使产品转型,用ID智能电动执行机构代替Al/MI智能电动执行机构是最佳选择。
但ID智能电动执行机构要推向市场,必须要对原有的产品进行优化,解决一直存在的一些技术上的问题,使ID智能电动执行机构以全新的面貌进入市场。
二、优化的内容
原有ID智能电动执行机构总体上应该说是成功的,但存在一些细节上问题,影响了整个产品的销售,主要突出在几个方面:
★力矩检测的稳定性
原产品中力矩检测的精度不高,安装调试麻烦,稳定性有问题。
★传动与间隙
间隙大小没有控制好,部分产品因锥齿轮啮合失效使整机阀位缺失
★密封性能 密封性能不好,出厂后有部分产品漏油、进水
★电气方面
主板无法兼容、电池容易损耗、校验设备不能校验ID的力矩。
针对以上的问题,必须在技术上加以解决。在孟厂长的亲自领导下,技术人员分成各个优化小组,分别攻关相应的问题。群策群力,刻苦专研,获得了重大的突破。下面介绍各个优化的内容。
2.1力矩检测的优化
★目标:
重点解决力矩传感器的安装,长时问动作以后力矩值的控制范围也不能有过大的偏差,保证系列产品的传感部件尺寸的一致性。
★解决方法:
★对轴承套孔进行控制的时候,因为要求较高,所以采用数控车削中心进行加工,并且在电镀时会出现电镀层堆积在压力传感器的安装平面上,导致轴承套孔的深浅不一,所以改变材料,免去镀锌。
★压力传感器与轴承套的精密配合,安装定位靠孔下的台阶,可免去用胶水固定这一步。保证了一致性,减少了对安装工人的要求。
★在未焊接压力板时可用专门的工装和测试设备检测额定负载下的压力值,减少报废率。
★在橡胶热片的选择方面,采用质地较软,能承受经常的正负压力而弹性不会有明显变化的材料,尽量与流体的特性吻合。
★选用合适的弹性热片,保证在不同的力产生的形变是线性变化,从而使作用在压力传感器上的力也是线性变化的。
★设计实验装置来保证检测精度
★优化结果:
通过上述整改以后,安装一致性较高,稳定性得到了较大提高。按照优化后的方案,完全可以达到设计和实际使用的需水。而且压力传感器也可以使用一个部件?
2.2产品间隙和锥齿轮优化
★目标:
解决锥齿轮啮合失效的问题,保证阀位的稳定性。
★解决方法:
★首先从尺寸和工艺角度对比了同类原装产品的大小锥齿轮传动结构与我厂大小锥齿轮传动的差别。通过测量尺寸差别来帮助我们分析我厂ID产品锥齿轮传动失效的原因。发现间隙有问题
★在铸造工艺对比中发现,我厂的ID锥齿轮无论从铸造的齿形,还是光洁度和材料,都和同类原装产品有差距,、ID的锥齿轮有齿形不均匀的现象,导致我厂ID产品的锥齿轮传动的流畅性不好。另外,齿轮表面不光滑,有的齿轮出现了整体变形。这些都是影响锥齿轮啮合的重要因素。
★在工艺方面,查询了相关资料,发现铸造工艺不同,压铸出的锥齿轮,由于温度、材料流动性等限制,会导致合金溶液在壁厚较薄的齿形部分流动不充分,引起齿形不完整、不一致的情况。而合适的铸造则可以有效的解决这一问题。
★优化结果:
结合以上分析,有针对性的从间隙和铸造两方面制定了优化方案。协作单位采用新工艺铸造出的大小锥齿轮,齿形明显有所改善,齿轮整体强度有所提高。改进后的锥齿轮和主轴前后共试制了两批样机(合计14台),一次性装两己成功,并分别进行正装、侧装、倒装等多位置安装,且每批次长期带载试验超过五万次。无论从锥齿轮啮合声音,还是阀位反馈方面,都未出现问题。对比之前车间生产时,大小锥齿轮会出现断裂失效,往往要有10%——20%的返工率来说,明显取得了突破性进展。
2.3 ID产品密封优化
★目标:解决产品密封不好造成漏油产品漏油、进水的问题。
★解决方法:
★首先分析了同类原装产品的密封情况,并比对我厂的ID,发现我们的产品与原装的在尺寸上的差别。并通过对ID箱体各个面的分析,总结出了哪几个面会漏油、进水。
★通过与同类原装产品分析,我们发现密封圈型号有差异,手轮与箱体之间的配合间隙过大。
★在对ID箱体各个面分析后,发现了另外4个地方也存在漏油的可能性。
★在止口面进水的问题上,发现接线孔的问题。
★手轮面进行改进,改变密封圈型号。
★对手轮的外径进行了改变,使手轮与箱体之间的晃动间隙减小,
★改变加工工艺,去倒角、毛刺去干净,加入质量控制点
★改变蜗杆的前端直径,改进安装工艺
★引入密封涂层来配合密封圈进行密封作用,
★修改配合尺寸,改进产品的装配质量。
★优化结果:
在提出了优化方案以后,用试验验证,总共装配了14台ID做试验。3台做进水试验;另外11台,分别进行正装、侧装以及倒装3种安装方式,在带负载的情况下,长期运转检查其漏油的情况。
在为期3个月的试验中,14台ID无发现漏油漏水的情况,、
2.4电气控制器的优化
★目标:
将技术中心控制板的电气接口和厂里目前控制板兼容,改变操作和显示方式,实现可互换,优化原控制板设计,
★解决方法:
★确定接插件的型号,将插件型号设计成一致
★分析信号定义,各个板卡之间及到接线盘的每根线的信号都确定下米。
★控制方式的确定,详细分析厂里控制板的控制逻辑,与我们目前的逻辑进行比较,确定存在的差异
★显示内容的确定,由于显示接口有差异,目前厂里的控制板为双显示屏,技术中心为单屏,为了一致性,对显示方式进行更改。
★操作方式的确定,对菜单的操作流程和显示内容进行了分析,确定了详细的流程图,除了对某些特殊的内容进行更改外,菜单显示相似度达到98%以上,操作方式完全一致。
★CPU的改进,选用可靠性更高的CPU。逻辑,与我们目前的逻辑进行比较,确定存在的差异
★显示内容的确定,由于显示接几有差异,目前厂里的控制板为双显示屏,技术中心为单屏,为了一致性,对显示方式进行更改。
★操作方式的确定,对菜单的操作流程和显示内容进行了分析,确定了详细的流程幽,除了对某些特殊的内容进行更改外,菜单显示相似度达到98%以上,操作方式完全一致。
★CPU的改进,选用可靠性更高的CPU。
★控制线路改进,设计框架重新编排。
★改进低功耗设计,降低电池功耗。
★把遥控器的硬件解码改为软件解码,解决采购上的难度。
★改变鉴相和缺相的方法,减少了硬件。
★断电后能一直显示阀位,功耗更低。
★液晶显示器宽温设计,高低温均能显示。
★提高力矩采样精度。
★加人多种抗干扰措施,提升可靠性。
★故障检测种类增多,有效保护。
★优化结果:
板卡全部实现了互换,接线全部统一,通过全性能实验,小批量试制了20台。经过3个月的长期运行,可靠运行,性能比原控制板有提升。
三、优化的结果
在孟厂长的带领下,通过全体技术人员的努力,ID智能电动执行机构优化取得了很大的成功,ID产品获得了新生,为十一厂的发展和转型提供了强有力的支持。ID产品推向市场后可能还会发生一些没有想到的问题,但只要我们发扬这次在优化中体现出来的刻苦专研,团结合作的精神,相信一定会把产品不断完善,给客户提供更好的产品,为厂里赢得更大的市场,为公司赢得更大的效益!